ComBio, Brazil
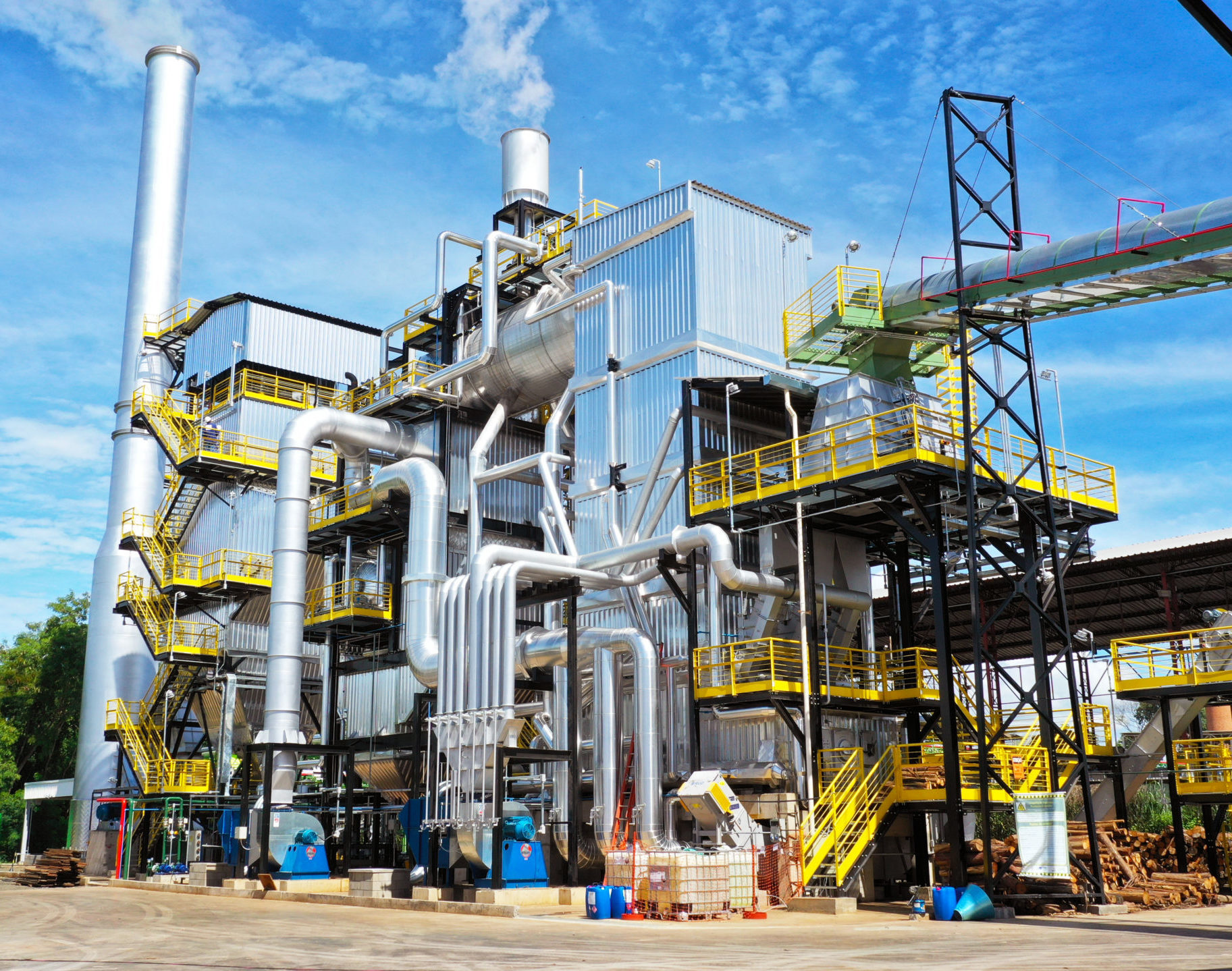
Situation BEFORE Aerovit Installation
ComBio Energia S.A. develops steam generation projects and cogeneration of electricity with biomass that promote environmental improvements and significant cost reductions for customers in the industrial segment.
The boilers supplied by DanPower and operated by ComBio burn several types of biomass, which changes the requirements of the process itself, because the soot deposition rate in the boiler thermal exchange tubes varies according to the type of biomass used. If nothing is done to prevent the accumulation of soot in the thermal exchange pipes, the efficiency of the boiler will decrease over the operating time and negatively impact the availability of steam and, especially in the case of ComBio, also impact on revenue.
At Klabin S.A., ComBio uses wood chips and sugarcane bagasse as fuel. It is estimated that this biomass mixture would require a total stop of the steam generation plant every 3 months for cleaning the boiler pipes.
Due to Klabin S.A.’s requirement for steam availability in the production, ComBio would prefer to have only one annual shutdown in order to deliver a high steam production while ensuring a high profitability.
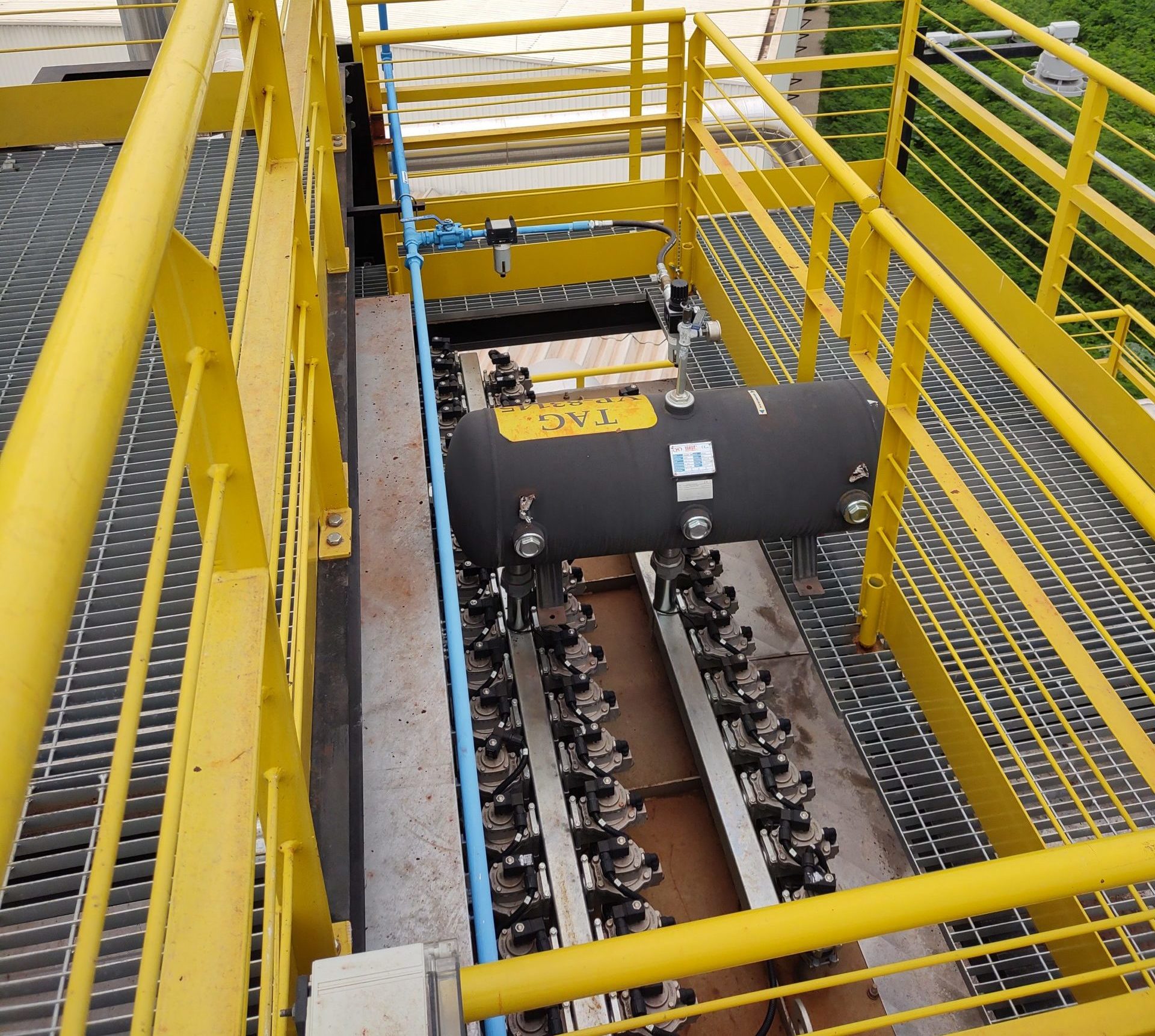
Situation AFTER Aerovit Installation
Through DanPower, one of the largest and most renowned boiler manufacturers in Brazil, ComBio was presented to Aerovit solutions for automatic boiler cleaning and decided to install the soot blowing system at Klabin’s plant to test whether the solution could, in fact, avoid unnecessary downtime and reduce the need for manual cleaning.
- The boiler in this case study is a mixed type, with a generating capacity of 37 tons of steam per hour and is equipped with an Aerovit soot blowing system with 49 valves in its firetube section.
- The valves are installed at the top of the rear smoke box, mounted on a grid of pipes, which function is to ensure the ideal distance between the soot blower system and tubeplate, to ensure maximum efficiency of the blowing operation.
- The steam generation plant was put into operation in February 2021, and after one year of continuous operation it was found that the boiler tubes still remained satisfactorily clean, requiring little effort during the annual manual cleaning operation.
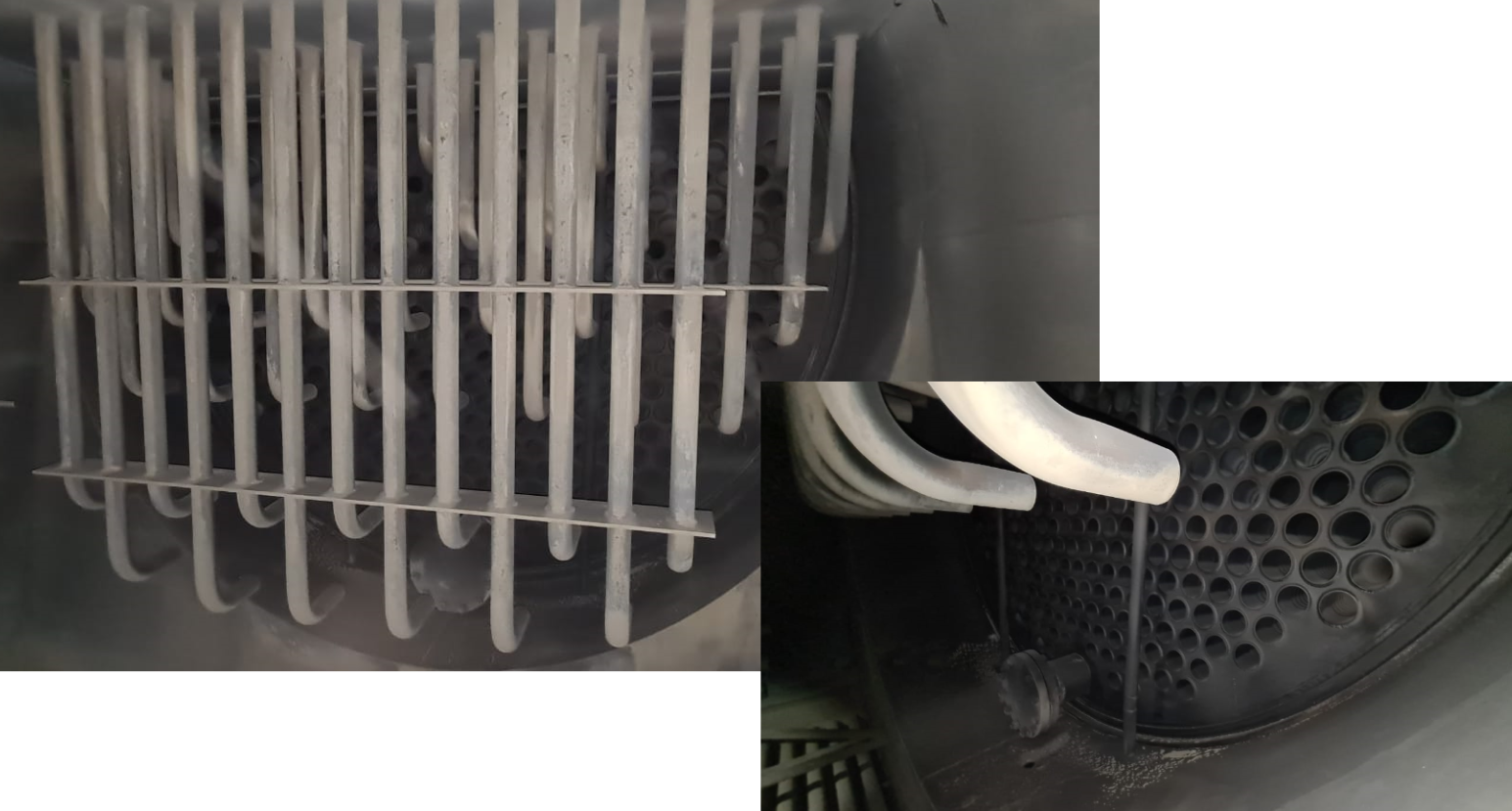
Statement from ComBio
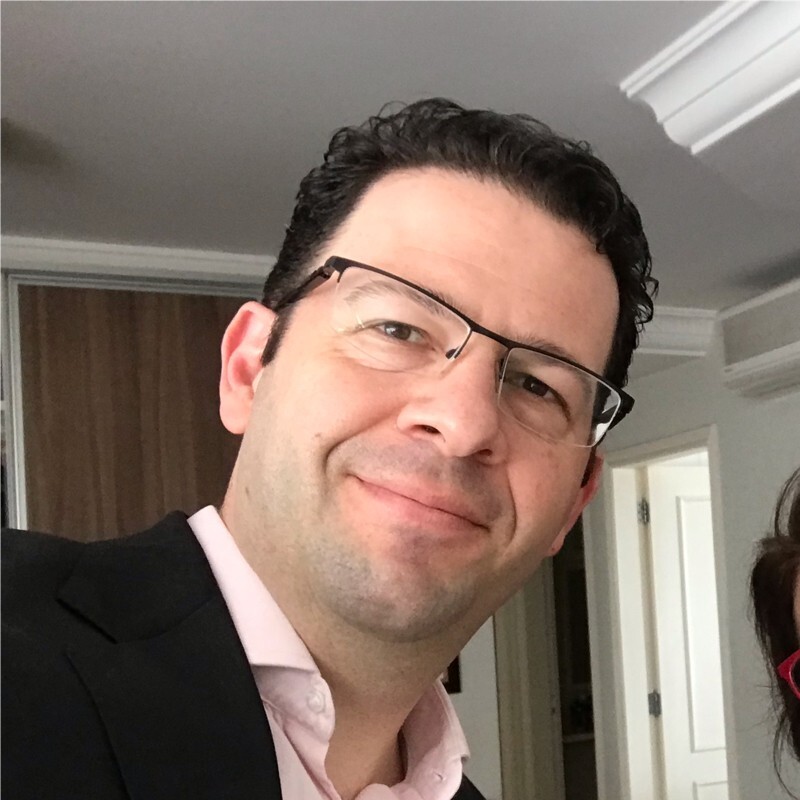
Download case
If you want further information about the case you can find it here