DLG, Denmark

The Challenge
The boiler, fueled by a challenging mixture of seed, grain, feedstuff residue, dust, chaff, and pressed grain, quickly developed severe fouling in the tube passes.
As a result, manual cleaning was necessary every 14 days, requiring eight hours of labor each time. Each cleaning operation led to 24 hours of downtime, amounting to a total loss of 624 operating hours annually.
This frequent maintenance not only resulted in high labor costs but also caused a noticeable decline in boiler efficiency, particularly in the periods leading up to each cleaning.
Additionally, increasing environmental and emission requirements placed further pressure on the facility to enhance its operational performance.
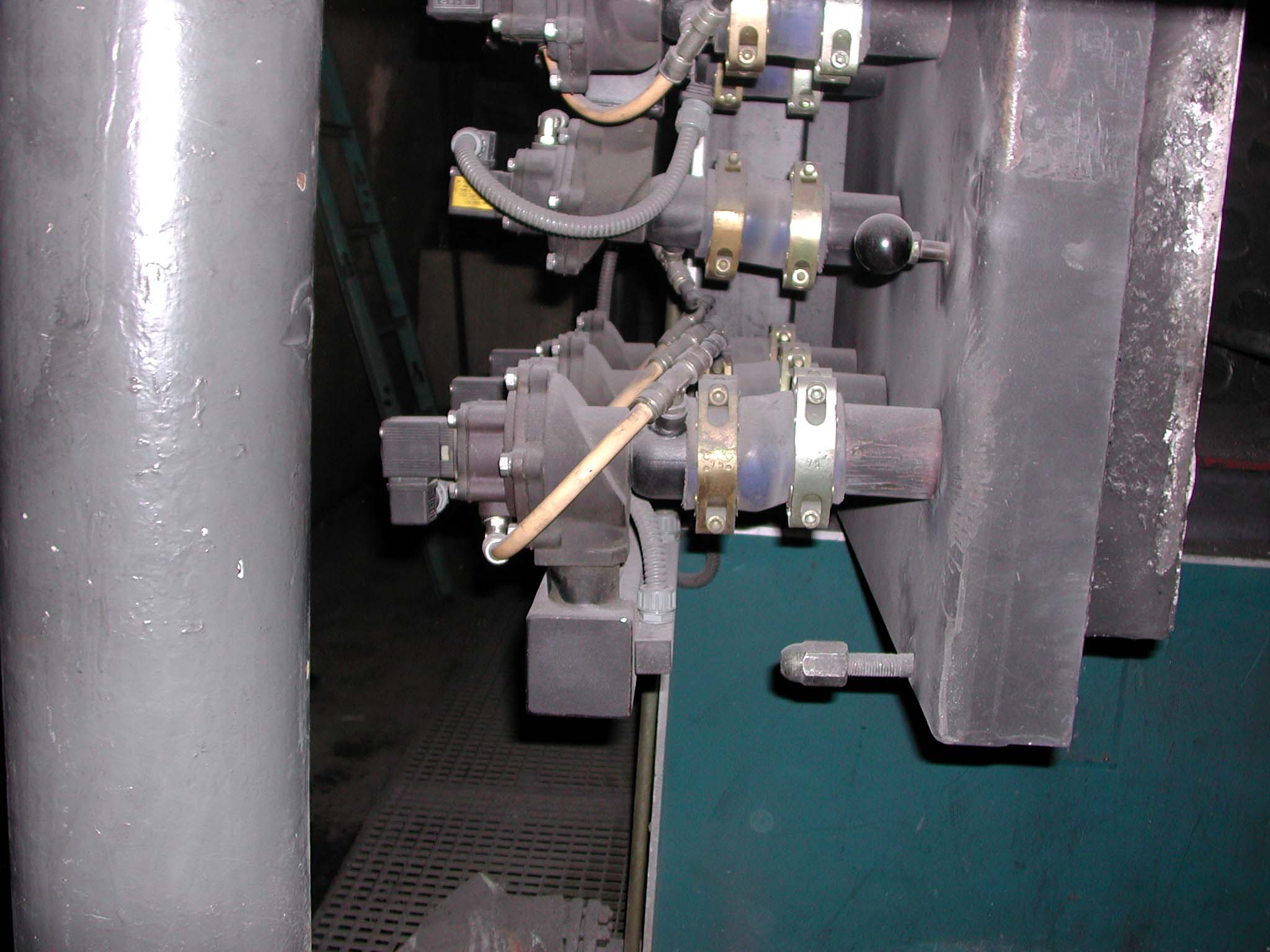
The Solution
DLG decided to retrofit the Aerovit ShockClean System to automate cleaning processes and optimize boiler performance. The system was installed on their Danstoker Multimiser No. 19, a 2 MW, 5-pass hot-water boiler.
The investment of 22.800 EUR paid off quickly, achieving a payback period of approximately eight months through improved operational efficiency, reduced downtime, and increased boiler capacity.
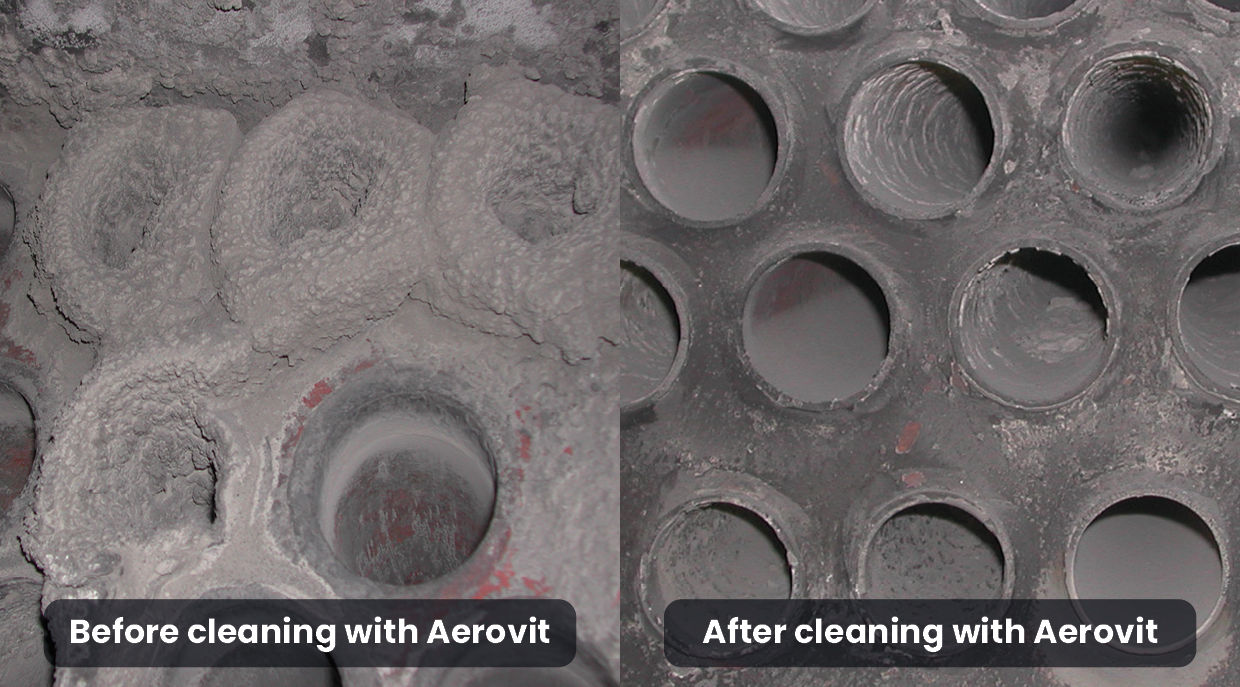
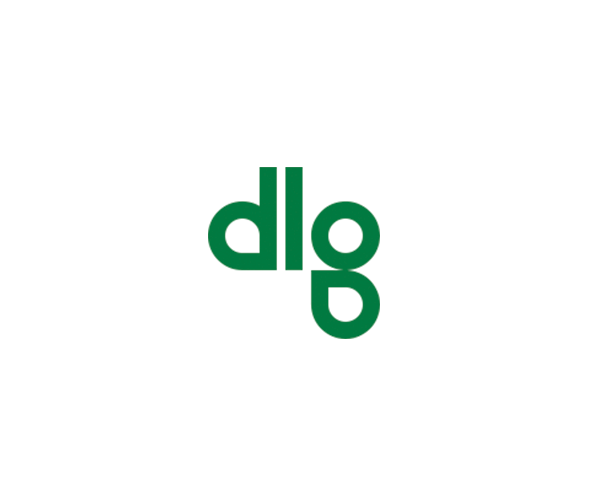
The Results
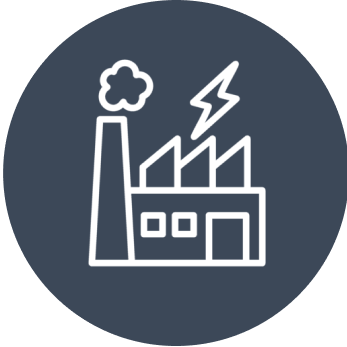
Reduced Cleaning Frequency
Manual cleaning dropped from 26 times a year to just 4 times annually.

Minimized Downtime
Downtime decreased from 624 hours to 96 hours annually. Which results in a saving of 528 operating hours (~84.6% reduction).
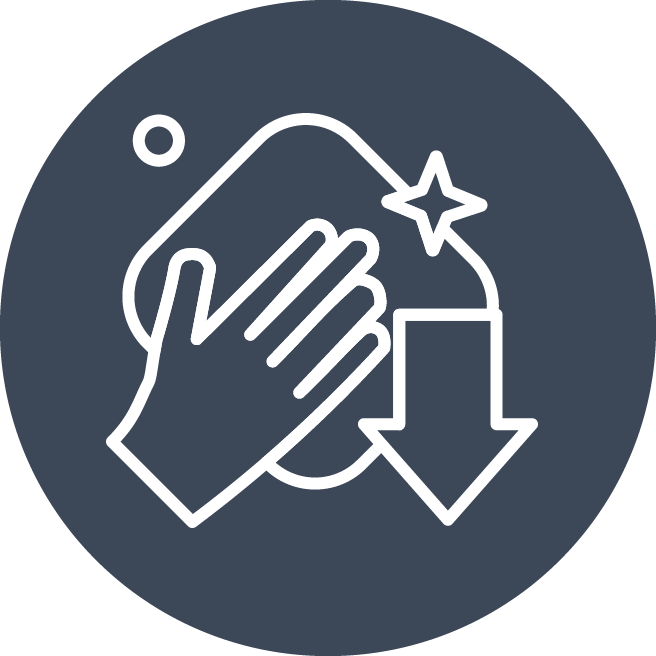
Saved working hours
Cleaning-related labor reduced from 208 hours to only 6 hours annually (~97.1% reduction).
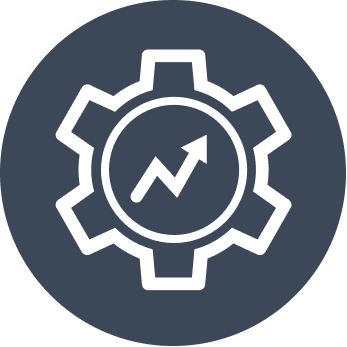
Increased efficiency
Boiler efficiency improved by approximately 8%.

Financial savings
Additional operating time and reduced labor resulted in savings of approximately 33.500 EUR per year.
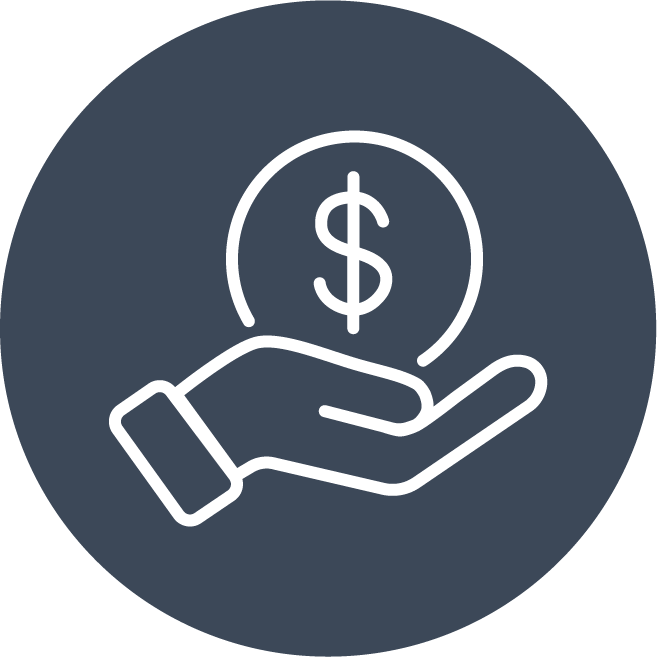
Rapid return on investment
The return on investment (ROI)was achieved in approximately eight months.
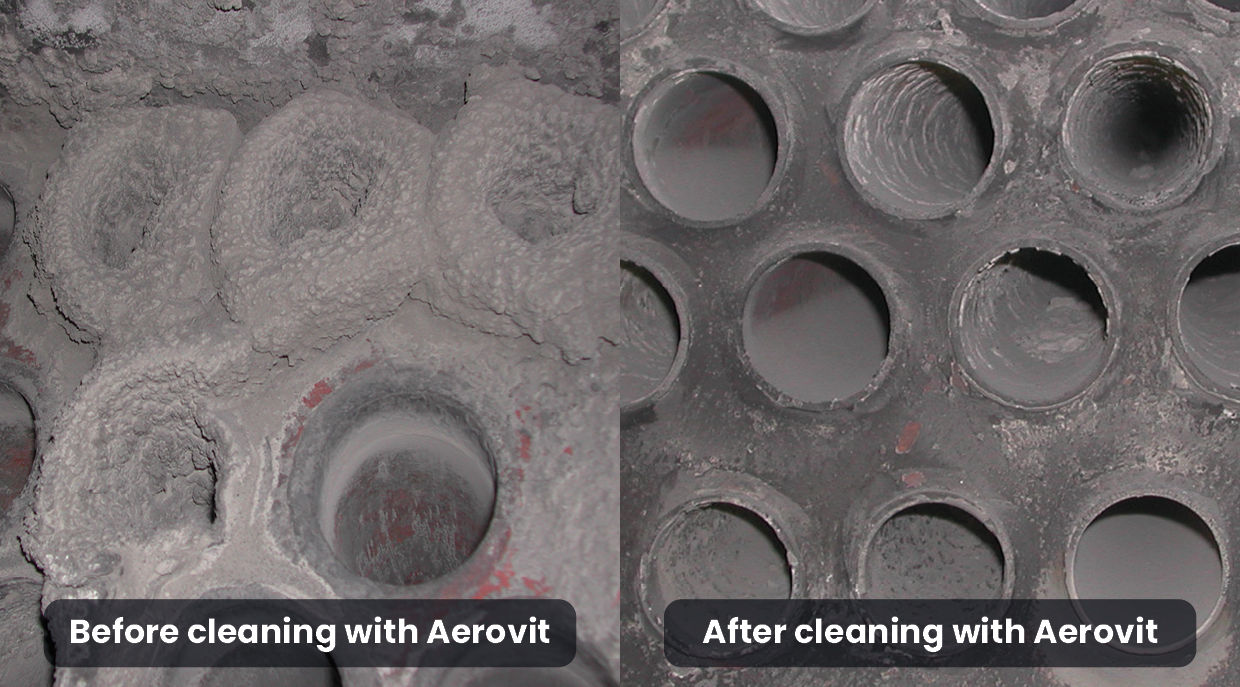
How does Aerovit ShockClean System work at DLG?
The Aerovit ShockClean System uses controlled bursts of high-pressure air (operating at 8 bar) to continuously and effectively remove soot deposits from boiler tube passes.
By maintaining clean heat transfer surfaces, the system ensures stable boiler operation, optimal flue gas cooling, and minimizes pressure fluctuations.
The system is installed externally and operates during boiler runtime, allowing facilities to maintain performance without interrupting production for manual cleaning.
Overview
At DLG’s waste-fired facility in Hasselager, Denmark, heavy fouling from problematic fuel mixtures led to frequent and labor-intensive manual cleaning of their Danstoker Multimiser No. 19 boiler.
To address the operational challenges and environmental requirements, DLG retrofitted the Danstoker boiler with Aerovit ShockClean System. The installation resulted in significant improvements in boiler efficiency, operating hours, and cost savings.
Download the case story
Discover how we helped DLG to reduce manual cleaning and increase efficiency.