HEM, Sweden
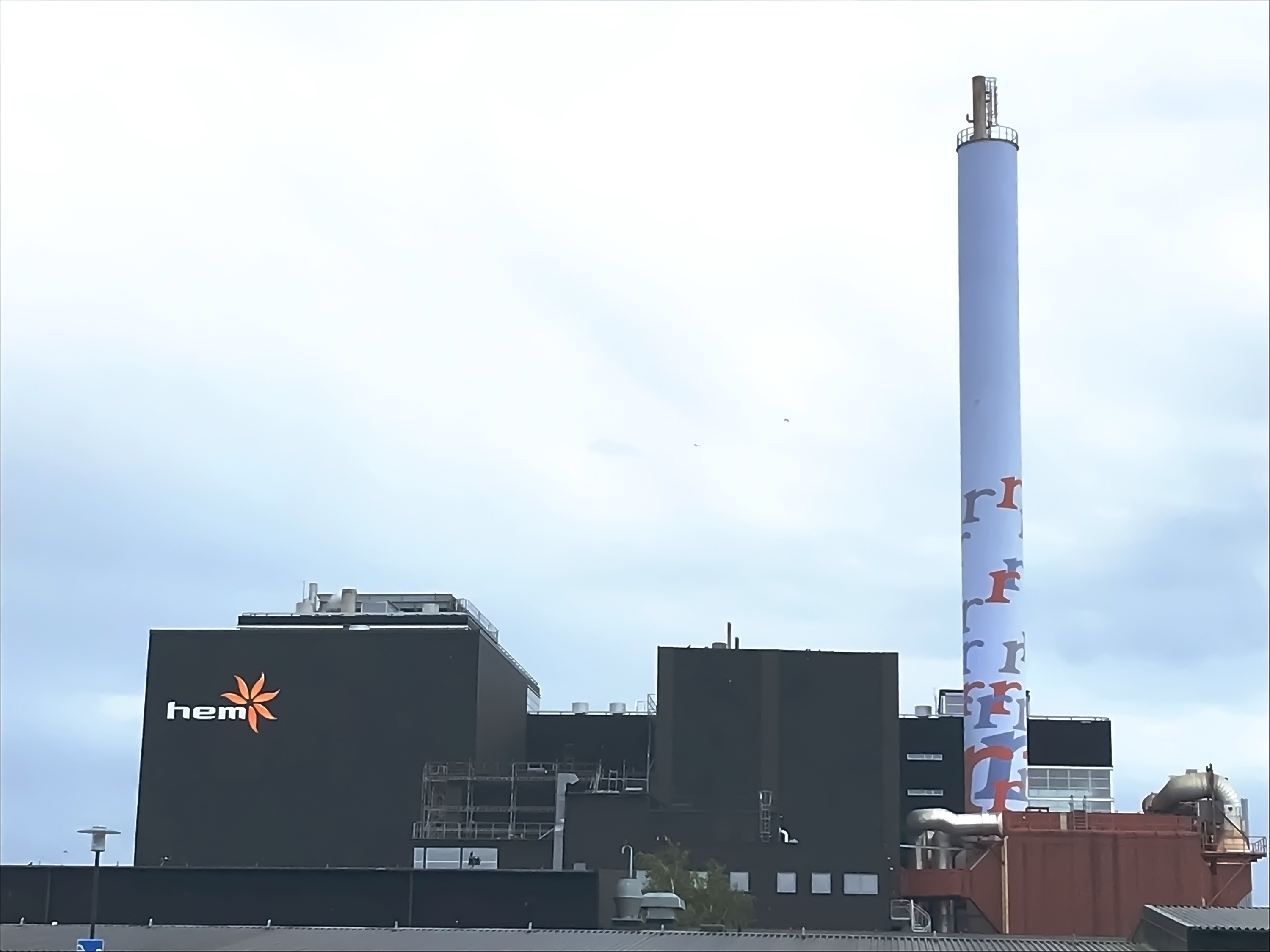
The Challenge
Keeping the heat exchange surfaces in the boiler clean is crucial for producing steam and hot water at a co-generation plant like Kristinehed. To ensure efficient heat transfer, a water shower cleaning system was installed in the empty passes 2 and 3 back in 2006.
After some years, soot deposits began to build up more frequently, which required an increase in the number of soot cleanings to as much as three times per day, yet only a minor decrease in flue gas temperature was achieved.
The maintenance team then sought a solution and discovered the rotating SC-jet nozzle head. They began by testing the nozzle head attached to the existing water shower cleaning system and immediately experienced a significant cleaning effect along with a clear decrease in flue gas temperature.
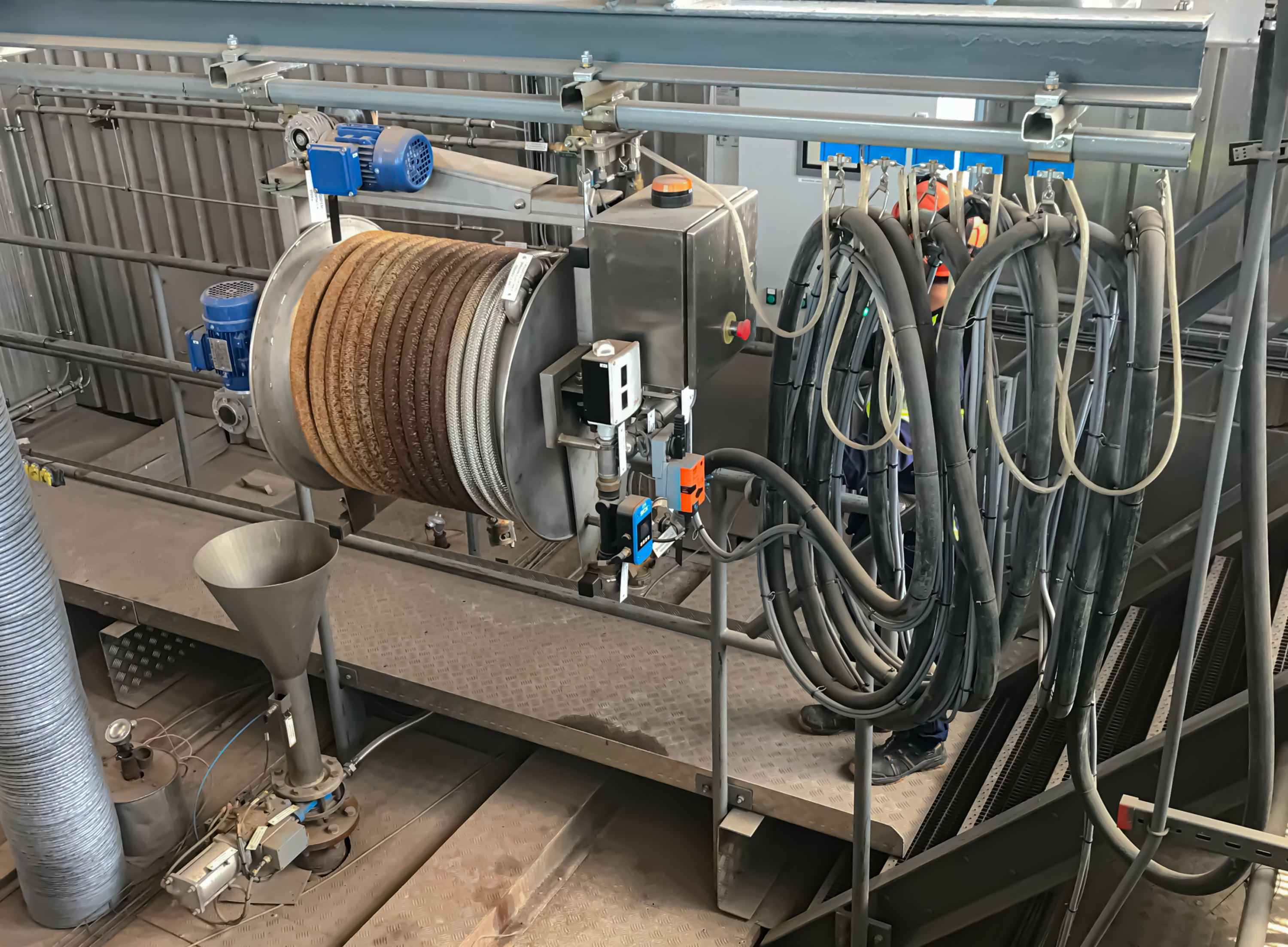
Solution – Aerovit SC-Jet Shower Cleaning
In 2021, the Kristinehed co-generation plant decided to implement the fully automatic Aerovit SC-jet system in passes 1 and 2 and a semi-automatic Aerovit SC-jet system in empty pass 3, which yielded great results.
The frequency of soot cleaning in the empty passes decreased from 3 times per day to just 3 times per week which saved 86% of water. In addition they experienced noticeable drop in average flue gas temperature by approximately 65°C.
Since the introduction of the Aerovit SC-jet, the boiler has been able to operate seamlessly throughout the entire year without requiring any cleaning shutdowns.
Furthermore, this implementation has resulted in a remarkable enhancement of the boiler’s efficiency. Consequently, the boiler now generates a significantly higher output of megawatts per year, thereby increasing its overall productivity and reliability.
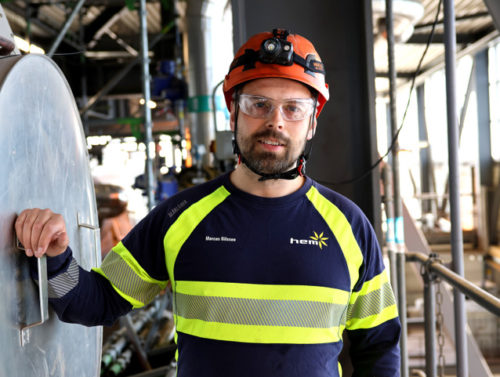
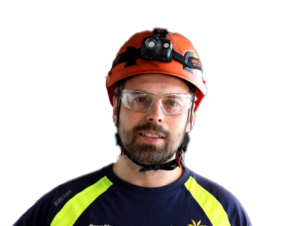
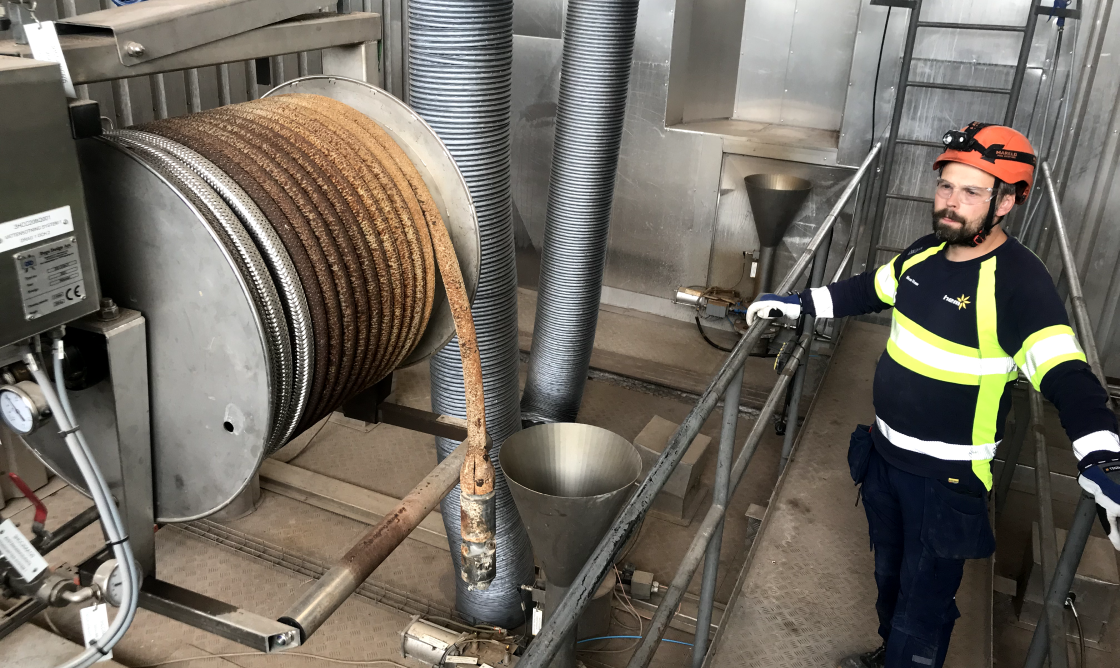
How does Aerovit SC-Jet Shower Cleaning work?
The Aerovit Shower Cleaning solution is an online system capable of operating effectively at high temperatures. At the Kristinehed co-generation plant, boiler cleaning is initiated when the boiler temperature exceeds 540°C.
Cleaning is performed by lowering the SC-jet nozzle head down into the boiler empty passes 3 times a week in just a few inlets due to its reach, up to 5 meters. During full-load operation of the incinerator, an optimal quantity of water is precisely sprayed onto the boiler walls, effectively removing the slag deposits. This process ensures efficient performance and is executed with precision.
The results
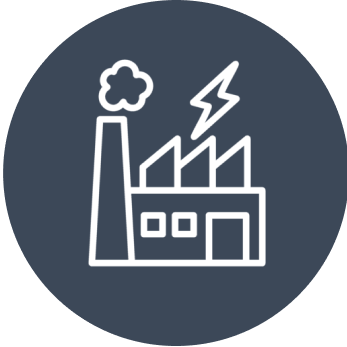
Flue gas temperature reduced by approximately 65°C
The installation of the SC-jet system has led to a significant decrease in smoke gas temperatures. Previously, the flue gas temperature ranged between 600-640°C. Now the temperature stays consistently between 530-580°C. This reduc- tion in temperature contributes to overall efficiency and reduces the strain on the boiler system.
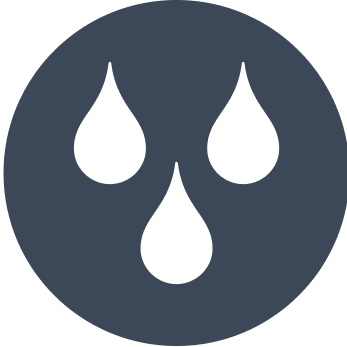
Reduced water usage by 86%
The SC-Jet system has significantly improved water usage efficiency in the cleaning process. It reduces water running into ash deposits and enhances evaporation, effectively removing soot from boiler walls. The cleaning frequency in the empty passes dropped from three times per day to just three times per week, saving 86% of water.
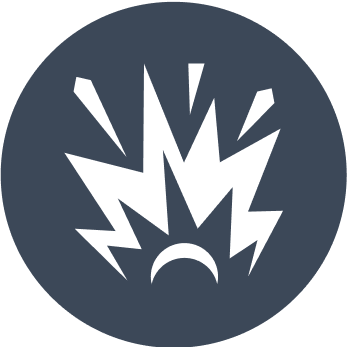
Saving € 21.000 annually on explosive blast cleaning
Previously explosive blast cleaning was used 10-12 times annually, incurring costs of approxi-mately 3,500 EUR per instance. With the intro-duction of the Aerovit SC-jet system, the fre-quency of explosive blast cleaning has been reduced to 4 times a year, saving in total €21.000 a year.
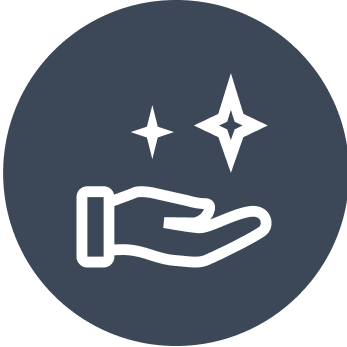
Reduced cleaning times by 75%
By cutting the number of water cleaning cycles from approximately 400 to 100 due to more efficient Aerovit nozzle head, the time spent on sweeping was reduced by about 75%. As a result of going from semi-automatic to fully automatic system around 150 man-hours of work were saved.
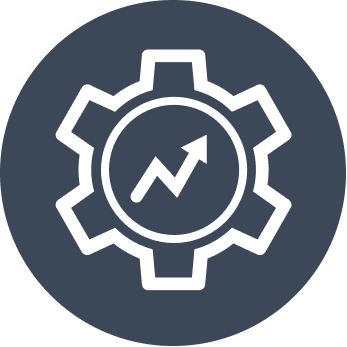
Increased maintenance efficiency by 75%
The SC-Jet system has improved water usage efficiency. Previously, changing the hose required 4 man hours, but now it only takes 1 man hour. This represents a 75% reduction in maintenance time. This leads to an estimated savings of 100 man-hours.
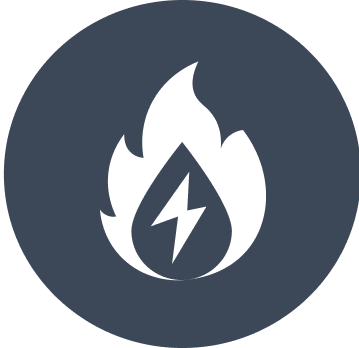
Higher Output
The boiler now generates significantly more megawatts per year, boosting overall productivity and reliability.
Overview
The Co-generation plant Kristinehed in Halmstad is located in the southwest of Sweden, providing district heating and electricity to the city of Halmstad. Its fuel source consists of 120,000 tons of combustible waste per year. The plant produces approximately 270,000 MWh of heat and 80,000 MWh of electricity annually
Download case
If you want further information about the case you can find it here